Accurate FOD Data + Thorough Analysis + Effective Action = Fewer FOD Incidents
Wherever aerospace products are manufactured or flown, a philosophy and culture of FOD Prevention spanning the entire operation is vital to assure product integrity, reliability, and cost savings. The exact costs of FOD can be hard to quantify because the “ripple effect” of even a minor incident affects many areas.
Suggested Resources
Check out our articles on What is FOD? or How to Set Up a FOD Program for more information.

While man-hours, component costs, personal injury or death are measurable, reduced customer confidence and lost business are nearly impossible to determine. We know that the implementation of an aggressive, well-structured FOD Prevention Program recently saved one aircraft component manufacturer over one million dollars in a single year and contributed significantly to increased sales.
Your FOD Prevention Program will bring you countless benefits. There are many elements to an effective FOD Prevention Program:
- Management Support
- Training
- Process Controls/Procedures
- Worker Involvement
- Motivation and Incentives
- Audit/Inspections
- Corrective Action/ Root Cause Identification
FOD incidents are danger signals of ineffective control methods or practices. Identifying the causes requires detective work and FOD analysis. Analysis requires data.
To be helpful, data must be collected regularly, recorded in a consistent format, and provided in easy-to-understand FOD Program Information Reports. These reports point to trends, identify specific problems and lead to corrective measures.
Accurate information is a major step toward arresting the villain: FOD.
Without it, other elements of your FOD Prevention Program may be misguided, and a waste of valuable time and resources. Developing a database that provides the necessary tracking requires forethought and planning but is easily managed using a desktop computer with spreadsheet (e.g., Excel) capability.
Determining the key data elements to track, who will collect the data, input and retrieve it, what formats are desired and who will receive/act on the information are all parts of the planning. The goal is to produce reports/charts in simple, usable language.
If Data isn’t understood, it is useless.
Management may want to see trends, set goals and recognize excellence. Supervisors and workers need specific information about problems within their units. Individual reports may be required to analyze a specific problem or gauge effectiveness of a corrective measure.
Therefore, different reports may be required from the same database. Once familiar with the procedure, you will find these FOD Program Information Reports surprisingly simple to produce.
Remember: the importance of data is to identify problems and implement lasting solutions.
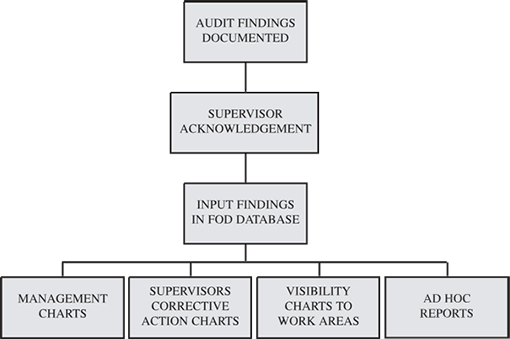
Sources of FOD Data
Audits & Inspections
Random daily checks of work and operations areas will assure compliance to standards, regulations or procedures. Develop an audit checklist that documents the date/time, auditor, shift, area and problem found. Use codes when possible to reduce the auditor’s time, ease data entry, and facilitate and standardize sorting the data for reports.
Incident Reports
FOD incidents (operation problems and system/component failures directly related to FOD) must be documented and investigated. An Incident Report form is used to document the problem and the findings. Enter information from the report into the FOD database to provide tracking/trending.
Customer Feedback
Products delivered to the customer are expected to be FOD free. If a customer discovers FOD in the product, immediately communicate with the source to implement corrective measures. Some manufacturers send a form or letter with the delivered product requesting a feedback report detailing the description and location of any FOD found.
A timely follow-up report to the customer affirming the corrective actions taken to avoid recurrence is good business practice. Again, the key data elements from the customer’s feedback report should be recorded in the FOD database.
FOD Database
Using Excel, set up a spreadsheet to record all the data elements to be tracked. Consistency and uniformity of codes used is vital for accurate sorting of the data when producing reports. Begin collecting data for a trial period before establishing the FOD database to assure that all the elements desired are included.
Charts & Reports
After the FOD database is established, data may be sorted on any of the parameters desired. Using Chart Wizard in the Excel program, select the chart type that best suits the type of report to be produced.
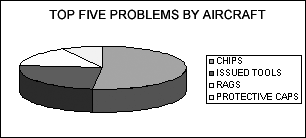
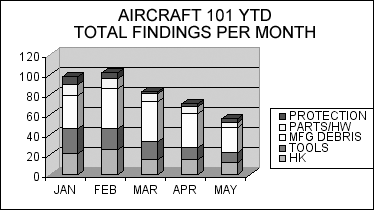
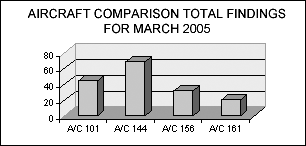
Chart A
Chart B
Chart F
Corrective Action
Problem resolution/corrective action is dependent upon the identification of the root cause (primary contributor). Therefore, information tracked in the FOD database must be as specific as possible to facilitate investigation. The root cause is sometimes difficult to determine and often intimidates the department and/or individual(s) that may be the origin of the FOD problem. Two techniques that help the investigator overcome these problems are the “Fishbone” and the “Five Whys.”
The Fishbone is a graphic breakdown of contributing factors to a problem.
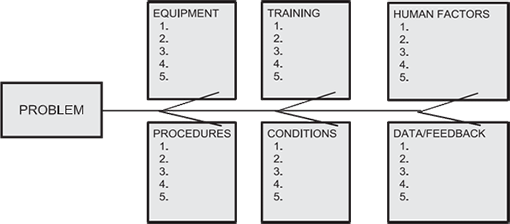
“The Five Whys” has been used by researchers for many years to analyze casual factors to complex problems. Generally, if all five stages of asking “why” to a problem are answered with conviction, the root cause will reveal itself.
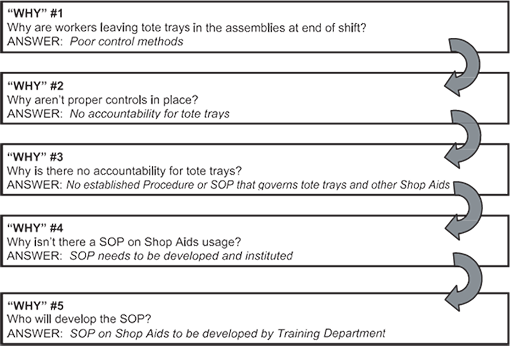
The “Fishbone” and “Five Whys” should be completed by the investigator for each incident or grouping of similar findings and reviewed/approved by management or a Corrective Action Board.
A Corrective Action Plan based on the root cause should be developed to avoid the recurrence of the problem. The Corrective Action Plan plots the planned steps or individual activity planned and assigns target dates for completion. A problem history should accompany the plan.
Ideally, a CAB (Corrective Action Board) will be established to review Corrective Action Plans and track problems to resolution. Convene this Board on a weekly or monthly basis to review the progress/completion of Corrective Action Plans, problems encountered by investigators and/or action coordinators, and problem recurrences. A formal review emphasizes the importance of solving FOD problems and validates/approves the initial plan and closure action. Periodic communication of the Board’s functions to all levels will remind everyone of the commitment to FOD Prevention.
Recurrence Control
Initial actions taken to solve a problem may not resolve the issue.
Maintaining a database of Corrective Action Plans allows recurring problems to be identified and reassigned. Use the information on the Corrective Action Plan for key data points. Using a problem code simplifies sorting the data over an extended time period. For consistency, use the problem codes on the Auditor’s Checklist.
Summary
Effective problem-solving requires a clear and vocal commitment from management because it occupies time, resources and budget to accomplish. Knowing the importance of data/tracking is vital for feedback to management and workers. Consistent, reliable data allows your operation to measure, act upon and prevent FOD threats. Convert data into easy-to-understand colorful charts that are distributed to management and posted prominently in high-traffic areas.
Charts should be updated weekly and maintained current. Serious problems should be documented and designated for action, root causes identified and effective corrective actions implemented. Progress and sustained excellence should be recognized. Worker involvement should be encouraged, documented and awarded when significant.
Following these steps, you can reduce FOD findings dramatically in a reasonably short time period. One example: A flight test program for a new military aircraft reduced FOD findings by 94% in two years.
Data that identifies problem areas and trends, provides visibility, and tracks problems to resolution is the key to effective FOD Prevention.
Today, the “Visible Factory” concept is an important aspect of setting targets and meeting goals used by many progressive aerospace companies. Visibility is the first step to understanding problems and their resolution. Charts and reports of trends and progress posted in each work area help maintain the focus on quality.
A comprehensive FOD Control Program based upon reliable data and an FOD analysis is the engine that propels you toward your goal of problem-free products and operations. Zero FOD is YOUR goal, and sound data coupled with commitment is a key element in reaching it.