How much does FOD cost the aerospace industry? During my two-year tour at Pyestock, I studied in detail the number of engines rejected for FOD in the Royal Air Force, the number of engine modules damaged, and the estimated cost.
I also sought information from other air forces and airlines to establish the hidden cost of FOD to their operations and understand the benefits of intake and engine designs that could reduce the hazard and lower the FOD cost.
Suggested Resources
Check out our articles on How to Prevent FOD at Your Airport or How to Set Up a FOD Program for more great ideas.
The cost attributed to FOD is dependent, first of all, on an open and completely honest reporting system that accounts accurately for all damage to engines and aircraft. In the Royal Air Force we have a reporting system that categorizes FOD into two areas:
- Damage resulting in engine rejection is category A.
- All other damage is category B.
Forewarned is Forearmed
Sadly, we did not, and to my knowledge, still do not, recognize FOD damage to aircraft, especially tires, as forewarning of damage to engines. Standard reporting allows the Royal Air Force to trace most engine damage, to rectify problems, and to record data that provides the feedback essential in problem solving. However, to reap the benefit and learn from experience, the reporting process must encourage all damage to be reported and, above all, it must be accurate. The reporting forms should be simple and relatively quick to complete.
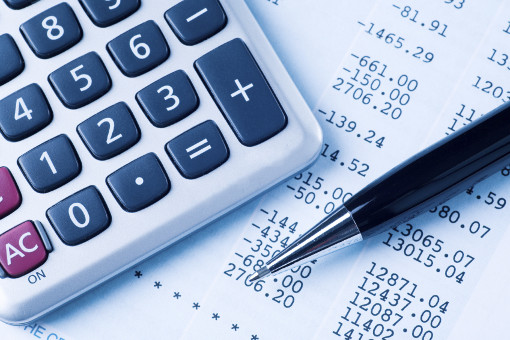
Unfortunately, for the people engaged in engine overhaul and module repair, FOD reports can become a tiresome hurdle. Hence, it is important that the results from their data are fed back to them promptly after being analyzed. Moreover, if discrepancy reporters may be punished, the system would tend to be misused, with the facts being only partially recorded, manipulated, or worse still, completely disregarded.
When gross negligence is the reason for the hidden cost of FOD, managers must require accurate reporting, not only to prevent recurrence but also to provide punishment to fit the crime. This is a continuing dilemma; balance must be achieved to gather as much information as possible without breaching confidentiality and trust.
As the pressure mounts to reduce expenditures, free and open reporting is a method on which future policy and management decisions can be based — a reactive system that can determine the heart of the problem and reduce its effects. It can influence designs for future air vehicles and engines. There is the potential of significantly reducing the problem where it is cost effective to do so; look at how the Russians have reacted to FOD — with intake doors and grids on the MiG-29 Fulcrum and SU27 Flanker respectively.
The Royal Air Force intends to get to the root of the problem by reporting all damage to engines and attaching a cost at source. I believe that their reporting system is unmatched anywhere in the world. Their enhanced reporting has already begun to allow the aircraft and engine designers to better understand the problem and influence their choice of design.
Understanding engine HCF (High Cycle Fatigue) is one objective. Plus, the FOD work is being used as an area for collaboration on the International Turbine Engine High Cycle Fatigue Science and Technology program (a joint venture between the US and UK military and turbine engine research communities). Although the ultimate aim is to eliminate FOD, in practice this is unlikely. But through meticulous housekeeping, we can reduce the problem for the benefit of everyone in our service and the taxpayer that supports us.
Realistic Calculations Validate FOD Prevention Programs’ Evolution
It was previously estimated in the 1990s that FOD was responsible for approximately $100 million in unnecessary costs and charges throughout the entire aerospace industry. This figure likely just scratches the surface of true costs, possibly covering the FOD price of a few of the replacement parts.
For example, in 1994, the Royal Air Force had at least 129 engines rejected for FOD from a combat fleet of 550 aircraft. Engine module repair and replacement cost about $30 million and, therefore, accounted for a huge slice of the operating budget. Moreover, the engine and repair contractor believed that the cost could have been as much as $70 million. This represented the cost of engine damage alone, and took no account of the damage to airframes, tires, or the unavailability of aircraft to perform missions.
If these additional costs were considered, the FOD charge to the Royal Air Force alone in 1994 could have been in the region of $100 million!
Projecting this example across the approximately 20 other air forces of at least equal size and force — there are probably many more today — creates a staggering figure of about $2 billion. Bear in mind that there are 172 air forces in the world, and to arrive at an accurate total, their FOD costs should be combined with the cost of FOD to the airlines of the world.
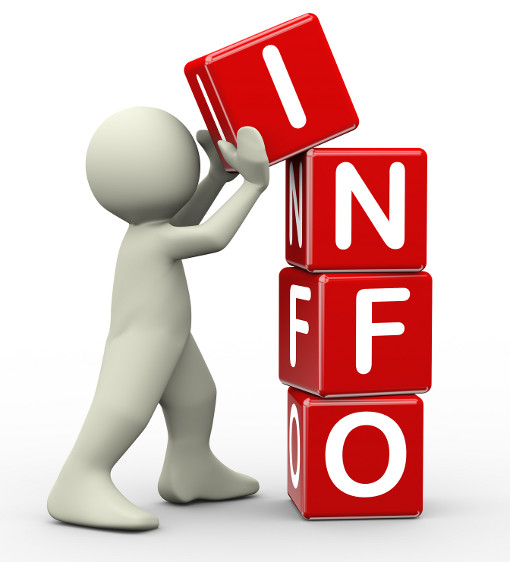
The Air Transport Association of America, which in 1996 had 23 airlines as members, recorded a three-year average of $7.4 million per airline per year in FOD, or $170 million per year overall, of which about $72 million was for engine damage. There are about 886 airlines, and approximately 100 were at least equal in size and operations to those member airlines of the Air Transport Association.
Therefore, applying the same FOD cost average per airline per year, the 100 airlines could spend up to $740 million for FOD. Add to all of this what FOD costs the thousands of companies in the world aerospace manufacturing industry, commercial aircraft and private aircraft operators, and the cost of FOD to the aerospace industry worldwide could well be in the region of $3-4 billion.
That’s Not All in the Hidden Cost of FOD
There are other costs that are not as easy to calculate but are equally disturbing. From accidents such as the Air France Concorde, Flight AF 4590, there is the loss of life, suffering and effect on the families of those who died, the suspicion of malpractice, guilt, and blame that could last for lifetimes.
This harrowing torment is incalculable but should not be forgotten, ever. If everyone kept this in mind, we would remain vigilant and forever prevent debris from causing a problem. In fact, many factors combine to cause a chain of events that can lead to a failure.
No matter where we fit in the aerospace industry, from the manufacturer to the end user — the customer — we must do all we can to reduce FOD charges for the common good of the industry and all that use it. We all have a part to play, but designers play a fundamental role in reducing the hazard and cost.
We no longer strive to improve performance regardless of FOD cost. We must focus on life cycle costs, and we must determine which design is best suited to the job and provides the most cost-effective solution.
FOD is a waste of resources. It is a threat to flight safety, and it requires maintenance downtime on many engines and components that would otherwise remain in service.
The discussion of FOD highlights the problem to everyone, and the assessment of the associated costs justifies decisions on design. With the right designs, FOD will have less impact on operations. With conscientious housekeeping, honest reporting, and meticulous analysis we will reduce hazards to everyone’s benefit.